Related Whitepapers
![]() |
MADE: Development of an Aerospace PHM Software Tool The Maintenance Aware Design environment (MADE) was conceived to provide a suite of software tools that could be used to design, assess and optimise Prognostics and Health Management systems for use in a wide variety of high risk industries where safety and reliability are critical, including mining, offshore and aerospace applications. MADE is currently being developed for application to aerospace systems and...Download The Paper |
![]() |
language of FMEA: effective use and reuse of FMEA data Practical uses of Failure Modes and Effects Analysis (FMEA) range from the identification of potential design defects and safety hazards, to maintenance planning, diagnostics and Prognostics and Health Management (PHM). According to the broadly accepted standard for FMEA, MIL-STD-1629A, a successful FMEA is one that conducted in a timely manner, so that the results can be used to.....Download The Paper |
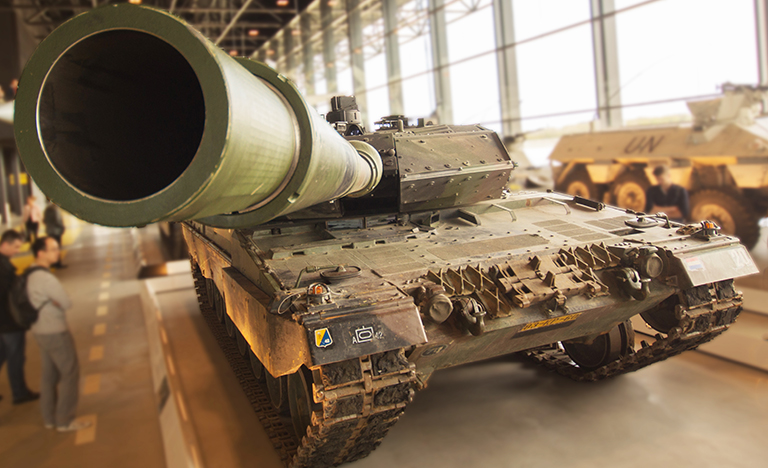
Maintenance Optimization of Legacy Army Assets
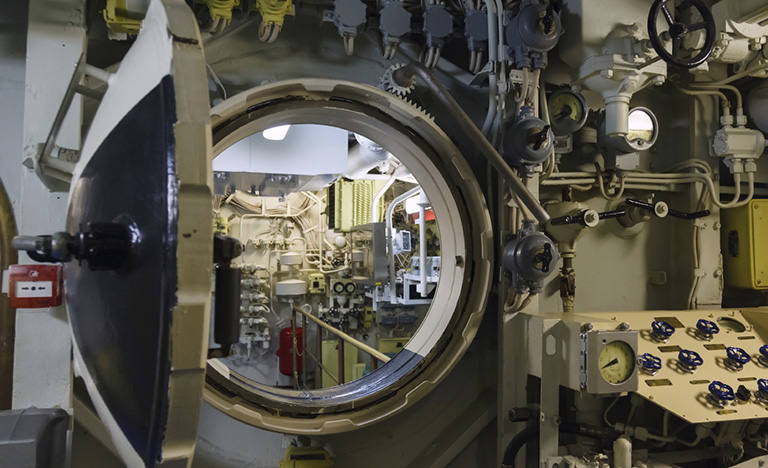
Maintenance Optimization of Legacy Maritime Assets
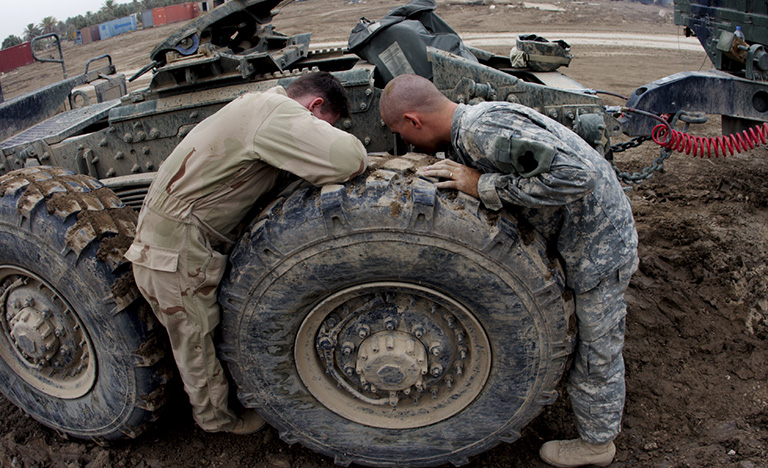
Establish Life Cycle Costs For A Bid / Proposal
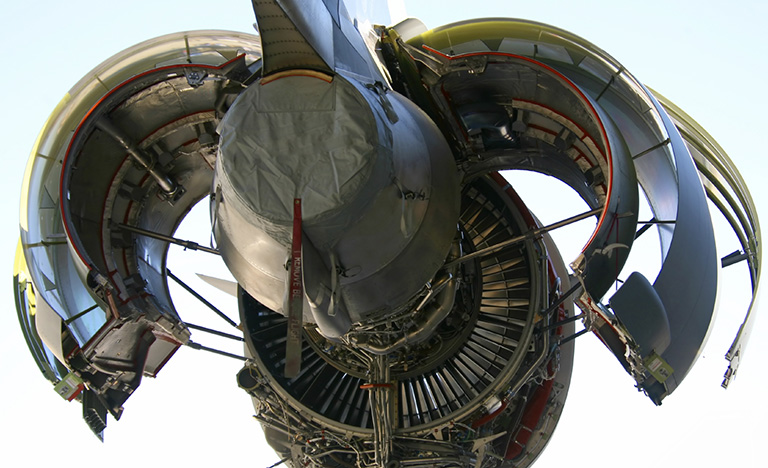